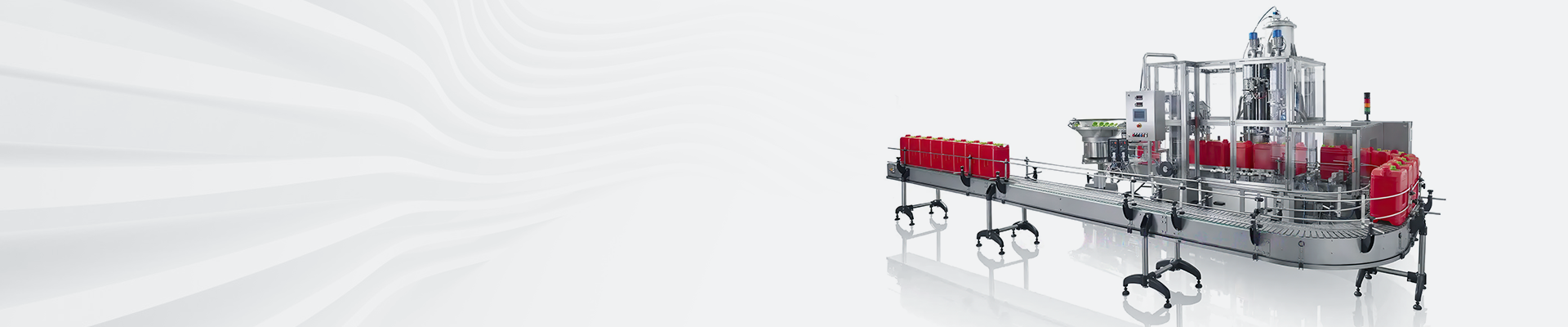
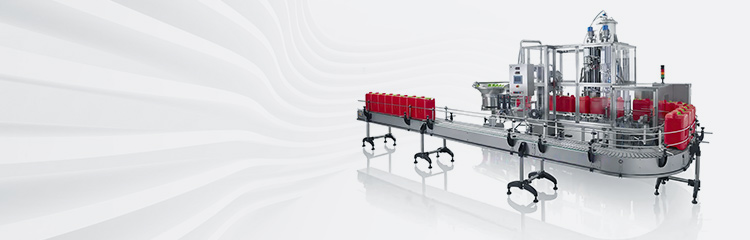
摘要:称重配料系统应用在石膏粉生产线上,通过计算机网络把各层连接在一起,完成数据采集和控制信息的传递。按一定顺序的动作,电动机启停和阀门开闭有着一定的顺序与连锁关系。
DCS系统是目前比较先进的配料系统,其主要优点是:可靠性高、分散危险、易于扩展、控制功能强、组态灵活、操作管理集中、人机界面友好。已成功应用于石化、电力、建材等行业。以某石膏粉生产企业4万吨系列石膏粉生产线的应用为例介绍了DCS的应用。
配料构成和功能
石膏粉主要工艺流程
(1)石膏块粗破、均化、细破:主要完成原材料的破碎,石膏块由粗鄂式破碎机进行初次破碎,在卸料场分区均化布置,再由细鄂式破碎机二次破碎,进入料仓。这一过程中,粗鄂式破碎机严禁带负荷启动,停车时要有报警信号;卸料场分为两个卸料区,卸料车要在两个区内自由切换,均匀布料。
(2)预粉磨环节:料仓出来的石膏粉经螺旋称、皮带秤进入柱磨机进一步研磨,再由选粉机选级分离,合格的物料通过转角螺旋输送机、垂直斗提机、仓顶螺旋输送机输送到生粉仓。在这一过程中,螺旋秤要定值计量并要求计算累加产量;柱磨机同样不能带负荷启动,而且需检测电流;由料位信号来选择仓加料。
(3)a粉反应车间把二水石膏进行蒸压、排水一系列物理化学处理,经过细磨系统和选粉,半成品进入混合仓。这一过程非常复杂,配料系统复杂,回路控制参数多,排水的工艺和设备是α半水高强石膏粉质量的关键,弄不好又转化成β型普通石膏。国内设备很难达不到工艺要求,设备多引进国外的,配料系统由厂家提供。
(4)在b粉车间石膏粉经过炒制变成半水石膏,后经细磨系统与选粉以后,半成品也进入混合仓。为了做到石膏脱水过程的精密控制,除了必须严格地控制炒制温度、出料温度及煅烧时间外,还必须严格控制物料进炒锅的进料量或进料的连续稳定性,尤其对于间歇式设备,必须严格地控制每一次的进料量(波动范围不能超过±100kg),并尽可能地缩短进料时间和出料时间。炒制过程中的每一个步骤都可能影响到产品质量,为了保证产品的质量及质量的稳定性,必须严格、精确地控制该过程中的每一个工艺参数。b粉炒制环节控制要求复杂,炒锅喂料称要定值给定,需检测锅内、炉膛、入口、尾气温度,风压、风流量,都是4~20mA的标准信号。(5)混合仓是石膏制品的深加工环节,不在本配料系统内。2.2、系统硬件的设计本系统采用了ABBIndustrialFreelance2000配料系统,该配料系统是面向工厂自动化的新一代开放式DCS系统。
石膏粉生产工艺
(1)石膏块的粗碎、均化和细碎:主要完成原料的破碎。石膏块首先由粗颚式破碎机破碎,均匀分布在卸料场,然后由细颚式破碎机进行第二次破碎,然后进入筒仓。在此过程中,禁止带负荷启动粗颚式破碎机,停机时应有报警信号;卸料场分为两个卸料区,卸料车应在两个区域内自由切换,以均匀分配物料。
(2)预粉磨:从料仓出来的石膏粉通过螺旋称重和皮带称重进入柱磨进一步粉磨,然后由分级机分级分离,合格的物料通过边角螺旋输送机、垂直斗式提升机和料仓顶部螺旋输送机输送到生料粉料仓。在此过程中,应在固定值测量螺旋秤并计算累计产量;配料机不能带负荷启动,需要检测电流。料位信号用于选择料仓进料。
(3)二水石膏在A粉反应车间蒸压排水,半成品经细磨系统和选粉后进入混合仓。这个过程非常复杂,配料复杂,回路控制参数多。排水技术和设备是α半水高强石膏粉质量的关键,如果不好就会转化为β型普通石膏。国产设备难以满足工艺要求。大部分设备从国外进口,配料由制造商提供。
(4)在B粉车间,石膏粉被炒成半水石膏,经过细磨系统和选粉后,半成品也进入混合仓在B粉车间,石膏粉被炒成半水石膏,经过细磨系统和选粉后,半成品也进入混合仓为了实现石膏脱水过程的精确控制,我们不仅要严格控制炒料温度,出料温度和煅烧时间,还要考虑物料进入炒锅的进料量或连续稳定性,特别是对于间歇式设备,我们必须严格控制每次的进料量(波动范围不应超过100千克),并尽可能缩短进料时间和出料时间炒制过程中的每一步都可能影响产品的质量为了确保产品的质量和稳定性,加工过程中的每一个工艺参数都必须严格和精确地控制。B粉油炸过程的控制要求很复杂,炒锅的进料刻度应设定在给定值。炒锅、炉膛、进气口和废气中的温度、气压和气流都应检测,这些都是4~20mA的标准信号
(5)搅拌仓是石膏制品的深加工环节,不在本配料系统中。
系统硬件
设计本系统采用ABBIndustrialFreelance2000配料系统,这是用于工厂自动化的新一代开放式DCS系统
DCS体系配料结构
根据给料系统的生产工艺特点和现场设备分布情况,建立了DCS系统的给料结构。
DCS系统的配料结构分为现场I/O站、过程控制级和运行监控级。称重控制系统通过计算机网络将各层连接在一起,完成数据采集和控制信息传输。
系统硬件配置
(1)过程控制站
过程控制站分为现场控制器和输入/输出站,现场控制器采用ABB称重,内嵌32位RISCCPU。3个I/O站,其中I号I/O站:原料破碎;II号I/O站:a粉车间;III号I/O站:b粉车间,完成现场信号采集和A/D、D/A转换等功能。
(2)DCS体系配料结构(2)操作员站(OS)
本称重系统安装了3台操作员站。操作员站选用适合工业现场的DELL工控机,硬件配置RAM256MB,硬盘40GB,19″彩色CRT;操作员可通过键盘与CRT与系统进行人机对话,完成对设备启、停、阀门调节,速度调节,过程参数设定,监视现场设备运行和显示过程参数、打印报表等。
(3)工程师站(ES)
该系统设置1台工程师站与1台操作员站兼用。工程师站可以实现硬件编辑、现场过程站编程、现场总线智能称重仪表组态、操作员站组态一体化编程及调试。
工程师站、操作员站、现场控制器和I/O站都安装在中控室。
(4)通讯网络
称重投料系统的通信结构由两层组成:第一层是现场控制层,实现控制器与I/O模块和智能称重仪表之间的通信。采用ProfiBus现场总线通信协议,传输介质为标准双绞线。现场设备状态信息和模拟信号通过这层网络实时传输到控制器;第二层为中央监控层,实现控制器与操作员站、工程师站之间的通信。系统通信采用TCP/IP协议以太网,传输介质为同轴电缆。通信速率10MB/S,传输距离可达1公里以上,抗干扰能力强。
异构系统之间的通信:在石膏粉生产线中,除了DCS以外,还有其他配料机。如精轧机配料采用三菱PLC(FXON-16EX),反应车间配料采用西门子S5-400PLC。DCS系统与这些系统之间需要进行信息传输和交换。DCS和PLC之间的互连方式为硬线连接,遵循Modbus协议RS-485串行通信。
系统软件ABBIndustrialFreelance2000提供了丰富的系统软件,可以完成很多功能,可以完成很多功能DigiTool61版本61软件安装在本系统工程师站,运行在WindowsNT40系统上,编程语言采用国际标准的IEC1131-3图形编程语言,功能框图FBD、梯形图LD、指令表IL和顺序控制图SFC不仅可以完成控制过程的组态,还可以进行工程调试和诊断功能。完成的组态结果由工程师站通过系统网络下载到相应的PS、FC和操作站OS。操作站配有运行监控软件DigiVis61version61,操作界面和菜单为中文。运行在WindowsNT40Workstation操作系统上的主要功能包括图形显示、数据监控、系统状态显示、趋势归档、记录、过程和系统报警、控制操作、系统诊断等。控制策略石膏粉厂整条生产线可分为原料粉碎、A粉生产车间和B粉生产车间三个区域,每个区域又分为若干组分别控制,整个配料系统分为粗粉碎组、细粉碎组和预粉碎组,这是原料粉碎系统的分组情况;粉末生产车间分为粉末反应车间进料组、粉末储存组、粉末细磨进料组和粉末细磨组;B粉生产车间分为铁锅给料组、B粉储存和混合车间、B粉细磨给料组和B粉细磨组,每个配料系统保持相对独立,当一个部分出现故障时,不会影响其他部分的工作,体现了DCS系统风险分散的优势。
(1)石膏粉生产中配料设备各部分的动作逻辑控制需要有一定的顺序,电机的启动和停止与阀门的开启和关闭之间有一定的顺序和联锁关系。为了保证生产过程的正常运行和设备的安全,必须严格遵守这些关系。称重控制器提供了这种顺序启动的“自动控制”理念。在中央控制室,操作人员可以通过键盘按顺序启动和停止一组设备,无需人工干预。在生产过程中,当某一设备发生故障时,控制器的联锁保护使相关设备停止工作。IndustrialIT编程采用IEC61131-3标准并支持逻辑梯形图。用LD语言编程可以很好地实现上述控制功能。
用LD语言编程时,配料运行返回信号的常开触点作为设备的启动条件,运行返回信号的常开触点作为称重设备的启动条件用LD语言编程时,配料运行返回信号的常开触点作为设备的启动条件,配料操作返回信号的常开触点作为称重设备的启动条件。配料设备之间存在相同的关系,这四个设备在配置时具有连锁关系和启动顺序。细分组有四个写变量,即STA1、STA2、STA3和STA4,它们分别作为设备4、3、2和1sta1、STA2、STA3和STA4的常开触点依次延时5s,这不仅保证了设备的顺序启动,而且满足了设备电机的启动要求。在配置期间,还有其他四个写变量,即STP1、STP2、STP3和STP4,它们分别作为设备1、2、3和4的停止条件。STP1、STP2、STP3和STP4的常闭触点依次延时5s停车时,停止装置1后,装置2、3、4可延时自动停止。
(2)计量控制系统控制对于累加和计量计算的问题,系统提供功能块,复杂的数学运算可通过组态完成。