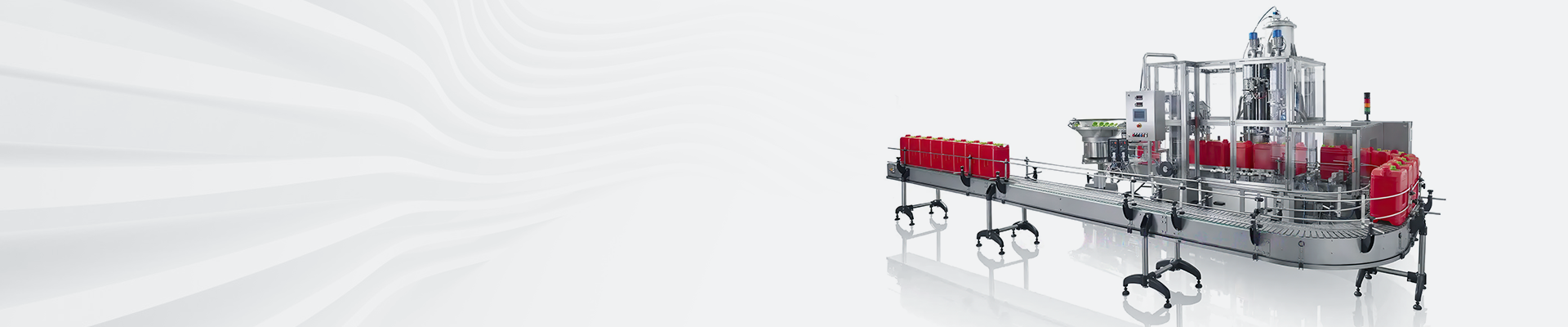
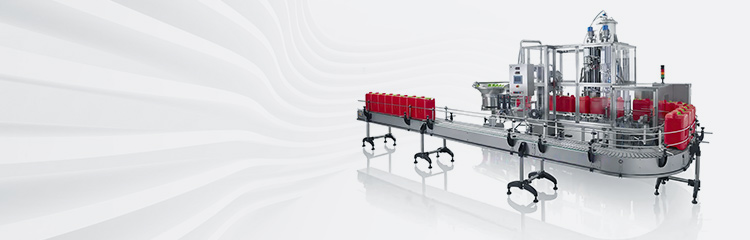
摘要:自动配料系统通过交流接触器控制各执行机构电机,由PLC和计算机共同组成对整个过程实现自动控制。采用自适应多级变速配料控制方法,实现变工况下不同配方配料参数的自整定,降低了从业人员的操作难度,提高了配料的精度和速度,从而提高了产品质量和生产效率。
目前国内饲料厂普遍引入自动化生产线,但配料系统的参数通常需要随着现场工作的变化(如配方变化)进行手动重置,因此即使是专业的调试工程师也很难快速设定最优参数,这对普通操作人员的要求更高,难度更大。这不仅效率低,可操作性差,而且配料精度波动大,严重影响产品质量。针对这种情况,设计了自适应多级变速控制自动配料系统,实现了变工况下配料参数的自整定,降低了员工的操作难度,提高了配料的精度和速度,从而提高了产品质量和生产效率,为饲料厂自动配料系统的设置提供了参考。
1饲料厂自动配料机的组成和原理
配料控制系统主要包括上位机、配料控制器、各种组分料仓、变频螺旋卸料机和控制阀组、配料秤和搅拌机等。控制器作为主站通过Profibus总线与上位机和配料秤进行通信。
加料系统的上层界面由VB编写,可以通过上位机下载配方和设置配料参数。配料控制器根据配方要求自动选择料仓,启动相应料仓下的变频螺旋卸料器和控制阀,同时读取配料秤的物料质量进行检测和判断,并根据自适应多速控制算法控制卸料器的转速,实现下料速度的控制。如果最终称重质量在允许误差范围内,它将完成该组分的下料,如果大于允许误差,它将发出警报,经操作人员处理后将该组分放入混合机,然后开始下一组分的配料。在下一批配料之前,系统将自动微调配料参数。所有成分称重后,搅拌机开始根据配方设置过程进行搅拌。
2多级变速配料控制策略的实现
配料过程的准确性和快速性是矛盾的。为了获得最佳的配料精度和速度,提出了多级变速配料控制策略,将配料过程分为高速配料、慢速配料和脉冲配料三个阶段。多级变速配料控制曲线包括卸料器转速曲线和配料秤物料质量曲线,其中快慢切换点、预切点、快慢切换时间、卸料器转速、最大配料脉冲数等参数可由上位机设定。
在配料开始时,卸料器的转速很高,此时配料秤的物料质量增加很快。在配料开始时,卸料器的转速很高,此时配料秤的物料质量在达到快慢切换点的质量时迅速增加,卸料器在快慢切换时间内完成快慢切换,而慢速配料的目标时间设置为t(t+t≤t)当质量p达到预切割点时,卸料器由于“空中下料”的存在而停止卸料,物料质量将在稳定时间结束时在稳定时间内增加,配料秤的称重结果应该有三种首先,它刚好在允许的误差范围内,说明这次设置的配料参数非常好,并且保存了当前参数;二是偏差过大,超过目标质量的正偏差,配料系统已无法调整这一结果,需要调整配料参数;第三,偏差过大且低于目标质量的负偏差。
卸料器主要用于设置三个参数卸料器主要用于设置三个参数预切割、公差和配料参数预切割部分用于设置快慢切换点质量、预切割点质量和预切割最大校正质量,需要注意的是预切割最大校正质量值该参数用于设置调整范围,防止优化时调整过度,这将在后面的校正公式中使用。公差设置部分用于设置质量的正负误差范围(即死区范围),在实际应用中可分为绝对质量误差和相对质量误差,取两者中较小的值。此外,该部分还用于设置系统的自动复位误差范围,也分为绝对误差和相对误差。当配料的实际质量与目标质量之间的差异超出死区并在自动重置的误差范围内时,系统自动接收质量以完成配料。如果配料的实际质量与目标质量之差超出死区,且不在自动复位的误差范围内,则系统输出报警,在进行下一批配料时,经操作人员确认后,配料完成,调整参数,最终使实际质量达到设定的死区范围;配料参数部分用于设置快速配料速度、慢速配料速度、脉冲时间等。
配料秤的界面主要用于设置配料监控参数、液体添加参数、配料参数和校正参数等四个参数配料秤的界面主要用于设置配料监控参数、液体添加参数、配料参数和校正参数等四个参数配料监控参数部分主要用于设置延迟监控时间、监控周期时间和稳定时间等参数,其中延时监控时间是指系统在此时间段内自动监控卸料器的卸料质量是否达到快速/慢速进料监控设定的最低进料质量,如果没有达到,则输出警报以提示物料短缺。稳定时间用于延时监控配料的实际质量并提高系统的稳定性;液体添加参数部分用于设置实际标定的单位脉冲液体质量,系统将根据采集的脉冲数计算添加的液体质量;配料参数设置部分用于设置排空监控周期、监控排空质量、最大排空时间、称重排空质量和称重排空延迟关闭时间等参数。
开始上位机设定的这些参数可以只是经验值,不一定是最优的。下位PLC接收初次给定参数后,需要在配料过程中不断优化快慢切换点质量和切断点质量,以获得最优的目标精度和速度。
3切断点的自适应调节
本文采用的自适应控制系统是基于模型参考的自适应系统本文采用的自适应控制系统是基于模型参考的自适应系统模型参考自适应控制系统由参考模型、放电器(被控对象)、实时质量反馈(配料秤的反馈信息)和自适应控制器组成,其中y(t)直接表示系统的期望输出,即各部件的目标质量;y(t)是放电器的输出,即每个组件的实际质量;它们之间的误差为e(t)输入(参考输入)R(t)是配料成分的实时质量根据输入和反馈的偏差,多速配料控制器控制卸料机的转速和相应的时间,即U,从而控制卸料机的输出质量y(t)如果参数设置得当,y(t)/在规格误差范围内一旦配方发生变化和卸料机速度发生变化,配料参数需要进行大幅度调整
此时,由于被控对象的初始参数是不确定的(或事先未知的),现场算子通常只能给出配料参数的近似范围,控制器的初始参数也不能很好地调整,因此在自适应调节器中引入自适应误差时,被控对象的输出y(t)与参考模型的输出y(t)之间的误差e(t)较大,通过自适应控制律的运算,直接改变多级连续配料的控制参数,并生成新的控制函数u(d)来控制被控对象,使得被控对象的输出逐渐跟随参考模型的输出,直到y(t)在规格误差范围内。
针对一次配料结束可能出现的两种情况进行分析并给出优化(修正)配料切断点和快/慢速配料切换点。
如果目标值(目标质量)不等实际值!(实际质量),“快/慢速切换点”和配料切断点都必须进行修正。实际情况分两种:一是实际质量偏小,修正值为正;还有一种是实际质量偏大,修正值为负。之间的质量变化曲线无需修改,故同时调整和位置,同时上升或下调位置。但为了保证稳定有序输出,每次操作只修正50%的偏差。此时切断点质量;修正值=快/慢速切换点质量P、修正值=AW。
目标质量和实际质量的偏差值,为最大偏差校正值(校正因子≤0.5)、c:为切断点质量最大修正值,这两个参数都是通过上位机预先设定。控制优化调整稳定性和速度。
如果实际质量符合公差范围,但测得的慢速传送时间(t)不等于目标时间(t加),说明切断点位置恰当,但是快/慢切换点滞后了,必须对“快/慢速切换点”进行修正,此时修正值为负。根据慢配料时间相对于慢配料目标时间的差异,分情况进行修正。快/慢速切换点重量P修正值用表示。
4运行效果分析
多级变速自适应配料系统运行过程中记录的16次配方和组分自动配料操作的数据,除初始设定参数出现正偏差外,系统立即进入参数自整定状态,第二次操作开始时的数据全部满足误差范围要求,第五次操作开始时的数据基本稳定在死区内,其中10个数据落在死区内,另外两个数据在正负公差范围内,表明自适应自动配料系统稳定且效果良好。多级变速自适应配料系统运行过程中记录的16次配方和组分自动配料操作数据,除初始设定参数出现正偏差外,系统立即进入参数自整定状态,并且第二次操作开始时的所有数据都满足误差范围的要求,第五次操作开始时的数据基本稳定在死区内,其中10个数据落在死区内,另外两个数据在正负公差范围内,影响实际质量和目标质量的偏差因素包括随机误差和系统误差。随机误差主要包括通风系统或振动扰动的影响、不同配方的组分质量、平均进料钩度和总质量对秤精度的影响。系统误差主要包括卸料截止时间、输送路径长度等,系统误差可以通过程序进行校正。
5结束语
该系统在使用过程中取得了良好的效果,降低了工人的劳动强度、提高了配料的精度和速度、增加了配方管理的灵活性、极大地提高了生产效率,为企业创造了良好的经济效益。