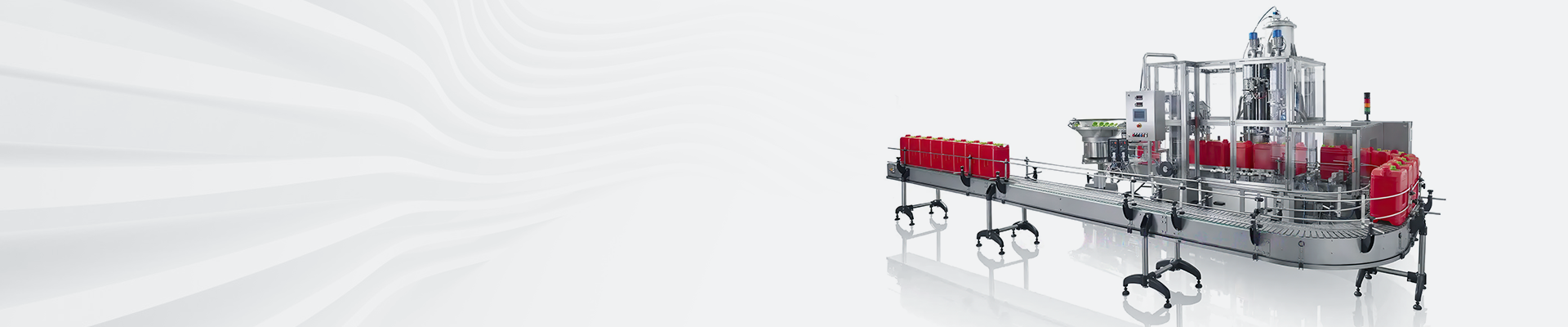
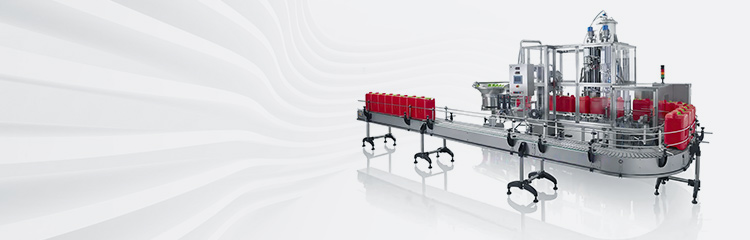
摘要:自动配料系统为带压密闭系统,以氮气为输送气体,输送的物料为粉末。物料自上游工段进入加料斗D-1A/B,通过料斗下方的旋转加料器RF-1A/B进入输送管线。系统的动力由压缩机C-1A/B提供,经过压缩机加压的氮气将旋转阀下管道内的物料送至目标料仓D-2A/B,完成输送任务。
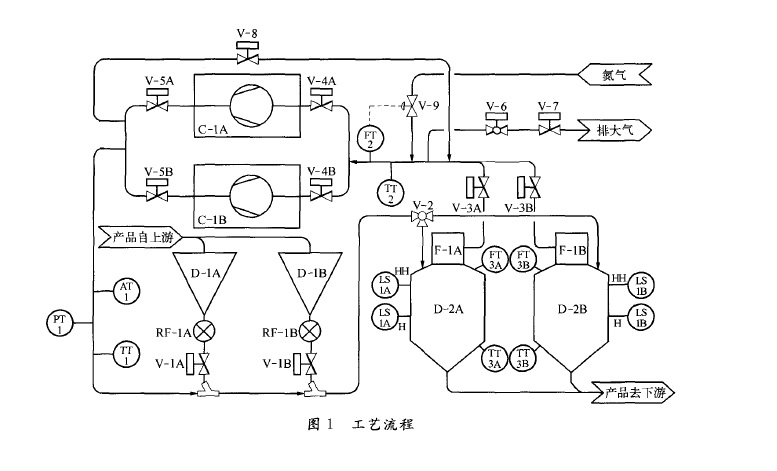
1问题的提出
气力输送工程技术是一项综合技术,涉及流体力学、材料科学、自动化技术、制造技术等领域。由于它具有布置灵活、高效节能、采用全封闭型管道输送,无二次污染以及自动化程度高等优点,广泛应用于石油、化工、冶金、建材、粮食等部门,是适合散料输送的一种先进技术。输送气体一般采用空气或氮气,动力一般由压缩机或罗茨鼓风机提供。气力输送系统根据工作压力不同,可以分为吸送式和压送式两大类;根据颗粒在输送管道中的密集程度,即固气比的不同,可以分为稀相输送和密相输送两大类。气力输送系统动设备较多,生产连续性要求较高,因此控制系统的合理性、可靠性及响应速度对整个气力输送系统的长周期稳定、安全运行起着至关重要的作用。本文将以压送式稀相输送系统为例,结合实际工程经验,从工艺流程、系统主要单元控制、系统软件的组态和编制以及系统试车运行等几个方面,对气力输送的自动控制系统进行讨论。
2工艺流程简介
气力输送系统为带压密闭系统,以氮气为输送气体,输送的物料为粉末。物料自上游工段进入加料斗D-1A/B,通过料斗下方的旋转加料器RF-1A/B进入输送管线。系统的动力由压缩机C-1A/B提供,经过压缩机加压的氮气将旋转阀下管道内的物料送至目标料仓D-2A/B,完成输送任务。氮气经过目标料仓上部的过滤器F-1A/B过滤后,返回至压缩机入口,循环使用。控制阀V-9所在管线为氮气补充管线,系统在开车初期或氮气压力不足的情况下由此管线向系统补充氮气。阀门V-6,V-7所在管线为氮气排放管线,当系统内压力过高时通过打开这2台阀门将氮气排入大气以降低系统压力。由于压缩机和旋转加料器为动设备,有一定的故障率且需要定期维护,这些设备均配置为一用一备。
系统在正常工况下为连续、自动、远程操作,因此配备相应的远程控制阀门和测量仪表。阀门主要采用带气缸执行机构的蝶阀和三通阀,通过电磁阀实现阀门的远程控制。在压缩机出/入口以及目标料仓上分别设置压力变送器(PT)、温度变送器(TT)用于压力、温度参数的测量。在压缩机出口设置氧分析仪(AT),检测系统内的氧气体积分数。目标料仓上不同高度设置有料位开关(LS),实现料位报警功能。
气力输送系统大致可以分为系统启动、系统正常停车和系统紧急停车三种工况。下面分别对这三种工况进行简要说明。
2.1系统启动
在系统启动之前,需要整个系统充满氮气,直到氧分析仪AT-1指示氧的体积分数小于4%。这个过程一般手动完成。由于所输送的物料为易燃介质,氧含量过高会导致物料在管道中摩擦起火。氧含量指标正常后,操作工在控制室内的操作站上选择输送路径,即选择所用的加料斗、旋转加料器、压缩机和目标料仓。选定后,所选压缩机出入口的阀门V-4A或B,V-5A或B打开,压缩机的旁路阀V-8打开,旋转加料器下方的阀门V-1A或B打开,三通阀V-2指向所选料仓,氮气回流阀V-3A或B打开。以上动作都是由程序自动完成的。至此,系统启动的准备工作已经完成,工艺操作人员在操作站上发出启动指令后,其启动步骤:启动压缩机;关闭旁路阀,系统预吹扫一定时间;启动旋转加料器,开始输送物料,系统启动完成。
2.2系统正常停车
正常停车是由工艺操作人员发出停车指令,其停车步骤:停止旋转加料器;系统进行清除吹扫一定时问,将留在管道中少量物料送入目标料仓;停止压缩机;打开旁路阀,系统停车完成。
2.3系统紧急停车
紧急停车是一种非正常工况,系统出现了异常情况,如温度、压力及氧体积分数等参数超标,或压缩机自身出现故障。在这种情况下,首先要考虑保护压缩机等重要设备的安全。所以一旦紧急停车情况发生,系统将自动同时停止压缩机和旋转加料器,打开压缩机旁路阀,使系统处于一种安全的状态。
3系统的主要单元控制
3.1系统的补氮和排放控制
对于密闭系统,压力是最关键的参数之一,对压力的有效控制关系到系统能否稳定运行。图1所示系统是通过阀门V-9来调节进入系统的氮气量,通过阀门V-6,V-7将氮气排放至大气。V-9是普通控制阀,V-7是普通蝶阀,V-6是1台特殊蝶阀,它的阀片中心有一个小孔。利用这几台阀的开关来控制压缩机入口压力PT-1.PV。
阀门状态监控功能,ZSO/ZSC为阀门限位开关返回的信号,FV-1A为阀门的状态变量,FV-1A为0时表示阀门运行状态正确,能够在规定时间内开、关到位,否则阀门故障。当控制系统发出开阀指令时,开始计时,如果在T内阀门的开限位开关返回信号,说明阀门打开,为FV-1A赋值0;否则为FV-1A赋值1,阀门关闭的过程也是一样。如果阀门处于故障状态,则输送系统将会停车,需要对阀门进行维修,排除故障。压缩机和旋转加料器的逻辑同阀门的类似。需要注意的是,T,T₂同设备的类型、设备的使用状况以及工艺的要求有关,只能通过对设备实际的操作和观察,逐步调整到一个合适的值。对于压缩机的旁路阀V-8的状态监控,阀开和关的时间是不一样的。V-8打开,意味着压缩机不带负载,是一种相对安全的状态。发生不正常工况时,首先打开V-8,以保护压缩机,因此V-8的开阀速度需要很快。在压缩机启动时关闭V-8,使压缩机带负载运行。如果管线中有堆料情况,V-8关闭过快会使压缩机负载急剧上升,导致出口压力过高而联锁停车。因此要求V-8要以一个比较缓慢的速度关闭。在阀门状态监控逻辑中,要对T,T₂设置不同的设定值。
3.3压缩机的联锁保护
压缩机是气力输送系统中最核心的设备,其联锁保护分为两部分:压缩机本体联锁和工艺联锁。
压缩机本体联锁是压缩机制造厂自带一个现场控制盘,对润滑油压力、电机温度以及出入口压力等参数进行监测,一旦这些参数超标,控制盘输出一个综合故障信号,要求在很短时间内停止压缩机,停车速度慢将有可能造成压缩机损坏。部分DCSI/O点的扫描速度是以秒为单位的,如果将综合故障信号送至DCS,经过逻辑运算后再向马达控制中心(MCC)发送停车指令,这个过程达不到立即停车的要求。并且,如果DCS出现故障而不能及时发送停车信号,压缩机的安全将得不到保障。最直接有效的方法是将压缩机综合故障信号送至MCC,使其成为压缩机供电控制回路的一部分,发生故障时同步切断压缩机的供电,达到立即停车的目的。
压缩机的工艺联锁是工艺过程发生异常而要求停止压缩机的运行。对于气力输送系统主要引起压缩机联锁停车的原因:压缩机出、人口阀门关闭;所选择输送路径上的阀门故障(上节所述);入口压力过高或过低;出口压力过高;目标料仓压力过高;系统内氧气体积分数过高。
3.4输送路径的切换
输送路径的切换主要包括旋转加料器和目标料仓的切换,这里主要说明在压缩机运行状态下的切换。旋转加料器的切换相对简单,只要停止正在运行的旋转加料器,等待一定的吹扫时间后,启动另一台即可。目标料仓的切换分为手动和自动两种模式。无论哪种模式,在切换料仓之前都应先停止旋转加料器,吹扫一定时间。在手动模式下,吹扫完成后,选择新的目标料仓,然后启动旋转加料器,切换完成。在自动模式下,工艺操作人员可以预选一台料仓,如果当前选择的料仓出现料位高报警时,系统可自动切换至预选的料仓。
3.5故障安全的考虑
故障安全就是当发生电源故障、仪表风故障以及控制系统元器件故障时,使系统处于一种相对安全的状态下。为防止仪表风故障,压缩机出、入口阀门V-4A/B,V-5A/B,压缩机旁路阀V-8,氮气回流阀V-3A/B等阀门要求为故障开AFO(AirFailOpen)。
旋转加料器和压缩机的正常操作都是由控制系统发出开、停车指令至MCC。为了防止MCC的强电压对仪表控制系统造成损坏,一般与MCC有关的信号都通过中间继电器进行隔离。根据压缩机控制电路的要求,停车信号要求为一个正脉冲信号。考虑到故障安全的需要,在设计控制系统时,控制系统的停车信号输出为负脉冲,对应继电器的输出连接常闭接点(此接点在线圈不带电时是闭合的)至MCC。这样设计的好处是,继电器在压缩机运行时线圈是带电的,当电源故障时,或线圈被损坏时,常闭接点闭合,引起压缩机停车,当然压缩机停车是一种相对安全的状态。
4控制系统的组态与编程
气力输送系统的自动控制是一种典型的顺序控制,其控制系统一般可以由DCS或PLC来实现。下边就以Honeywell公司的TPS分散型控制系统为例说明实现气力输送控制系统所要重点关注的几个问题。
4.1系统点组态
a)数字组合点(DC)。DC点可以连接2个输入和2个输出变量,用于对阀门、旋转加料器和压缩机等设备的操作。输入连接阀门的限位开关信号或动设备的运行状态信号,输出连接对阀门或动设备的指令信号。DC点有两种操作状态:手动和程序。当DC点置于手动状态时,可以通过DCS自带的标准控制面板对其所对应的单一设备进行开关或启停操作,这个功能用于单设备调试阶段,对设备的远程操作是非常方便的;当DC点置于程序状态时,只能通过CL(ControlLanguage,TPS系统自带的一种高级编程语言)程序或逻辑点进行开关或启停操作,便于顺序控制。通过DC点的应用,就可以实现阀门和动设备在手/自动两种状态下操作,便于系统单机试车和程序控制。
b)标志量点(FLAG)。标志量只有2个状态:0和1。标志量可以作为LOGIC点或CL程序的中间变量,也可以作为报警寄存器。
c)逻辑点(LOGIC)。与或非门及RS触发器等常规的逻辑运算都可以通过LOGIC点来实现。压缩机启动、停止联锁、阀门状态监测以及输送路径的选择和切换等逻辑功能都可以通过LOGIC点来实现。另外,LOGIC点还可以实现模拟信号的报警和联锁功能。
d)时间点(TIMER)。气力输送系统中有许多时间变量,如系统开车预吹扫时间,阀门和动设备的Watchdog以及系统停车吹扫时间等。这些时间变量都可以通过TIMER点来控制。TIMER点的设定值就是所要控制的时间,通过手动或CL程序可以启动TIMER点计时,当计时达到所设定的时间时,TIMER点的状态量翻转。通过这个状态量可以触发所需要的动作。CL程序中,也可以不通过TIMER点,直接对时间变量进行操作,但是使用TIMER点便于系统的调试和操作工的操作。由于时间变量可能会根据不同的操作条件而改变,也可以通过工艺操作经验的不断积累而进一步优化。工艺操作人员可以直接在点的细目画面上通过改变TIMER点的时间设定值来改变时间变量。因为修改CL程序中的变量,需要对CL程序重新编译下装,这个过程比较复杂,只有DCS维护人员可以做,工艺操作人员不能也不允许去做。
其他类型的点,如模拟量输入/输出点(AI/AO)、数字量输入/输出点(DI/DO)以及PID控制点(RC)等都是任何控制系统不可缺少的点,限于篇幅这里就不一一说明了。
4.2程序编制
TPS系统提供了CL程序和逻辑点两种工具来实现顺序控制功能。将CL程序和逻辑点结合起来实现气力输送系统的控制功能,可提高控制程序的可读性、可维护性以及方便工艺操作。
目标料仓的选择、压缩机的选择及联锁保护、旋转加料器的选择、系统的启动联锁、停车联锁条件及紧急停车动作,通过逻辑点组态实现。这样整个系统被分成几个相对独立的子系统,每个子系统用不同的逻辑点控制,同时系统中所有关于安全保护的功能均采用逻辑点实现。在系统调试阶段,可以对各个子系统单独调试,而不受其他部分的影响。系统的顺序开车和顺序停车步骤是通过CL程序实现的。在特殊工况下,如果需要手动操作输送系统,可以停止CL程序的运行,由操作人员按所需要的步骤操作,由于安全保护功能不是用CL程序实现的,这样在保证系统操作的灵活性的同时,又不会降低系统的安全性。
利用这种CL程序和逻辑点相结合的思路,在组态和编程时要注意以下两点。
a)CL程序和逻辑点是通过自定义FLAG点的传递有机结合的。这些FLAG点没有任何意义,仅起到变量传递的作用。对于这种FLAG点,只能由一个逻辑点或CL程序进行赋值操作,也就是说如果在程序中给它们赋值,则在逻辑点组态过程中就不能将该FLAG点作为逻辑点的输出,反之亦然。
b)在TPS系统中,CL程序的执行速度是毫秒级的,而逻辑点的扫描周期则相对要长一些。因此在编程和组态过程中,要注意到这个特性,采取一定的技巧,使CL程序和逻辑点运行同步。下面举个简单的例子说明这个问题。
5系统的调试与开车
5.1程序离线调试
在现场安装施工还没完成之前,可以对控制系统进行离线调试,这样可以检查组态是否正确,逻辑关系及顺序控制是否满足工艺的要求。离线调试可以在DCS上对现场信号进行模拟,以满足程序运行需要的条件。
5.2单机调试
在现场配料设备安装完毕后,可以对仪表、阀门、旋转加料器以及压缩机等设备一一测试。这个阶段可以检查仪表检测的信号是否准确,阀门是否在规定时间内开/关到位,旋转加料器以及压缩机是否能够正确启动、停止,压缩机组的联锁保护功能是否正确等。
5.3系统氮气试车
单机调试完成后,可以将所有的程序和逻辑全部投入自动状态,不带实物料进行试车。这个阶段可以进一步检查逻辑关系及顺序控制是否正确,可以实际进行压缩机、输送路径的切换,系统的顺序启动和停止,以及测试紧急停车功能。
5.4系统实料试车
因为实物料试车有很大的风险,第1次通常是手动操作的。首先手动启动压缩机。在启动之前由操作人员现场确认出、入口的阀门是否打开以防万一。当系统压力稳定后,可以关闭旁路阀,使压缩机带载。然后手动启动旋转加料器,打开D-1A/B上游的放料阀,进行物料输送。在输送初期应将上游放料阀的开度调小,使压缩机负载不要过大,待系统操作平稳后,逐渐加大送料量,直到系统的设计能力。当压缩机出口压力达到设计量时,标志着气力输送系统开车成功。
在系统试车阶段,应根据实际的操作条件,对系统的时间变量进行调整,如系统预吹扫时间,旁路阀的关闭时间,以及阀门的开关时间。这些时间都会影响系统顺序开车所需要的时间。如果开车所需的时间过长,将会导致气力输送系统上游系统料位过高而停车。
6结束语
本文讨论的气力输送系统是一个经过简化和抽象的模拟系统,仅包括了气力输送系统所必须的最关键的设备和仪表。实际上的系统比这个系统复杂,会有许多辅助设施,如换热器、过滤器、手动阀门以及旋转加料器和过滤器的氮气反吹控制单元等,料仓和输送路径的设置也相对复杂一些。同时,根据输送介质和工艺流程的不同,控制系统也会有一些差异。但是作者介绍的是气力输送控制系统最基本的实现方法和思路,还有一些在工程中总结出来的技巧,希望对实际工程化系统设计和实施有一定的借鉴和帮助。