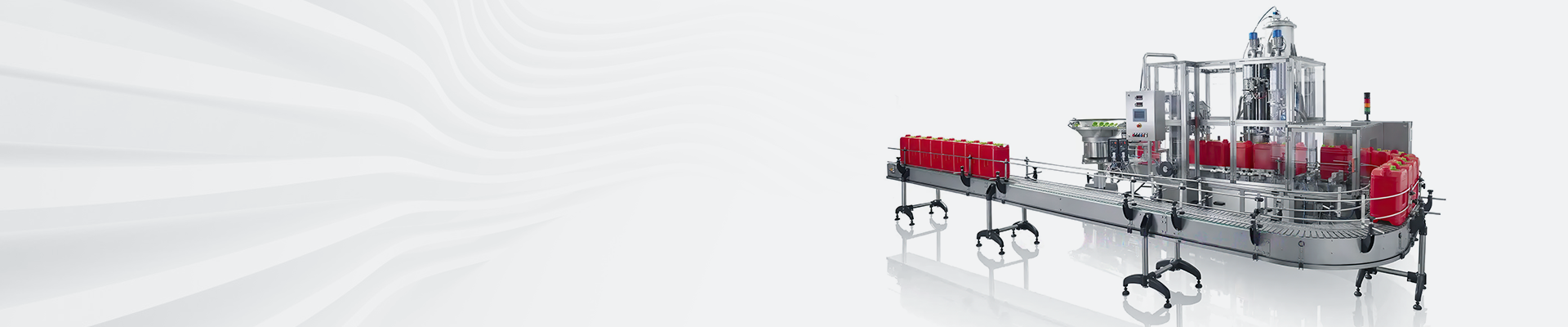
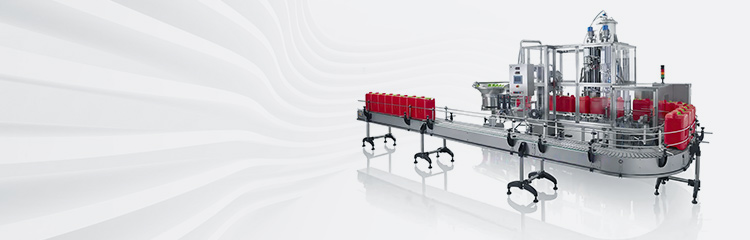
摘要:自动配料系统采用现场总线控制&分布式I/O结构,实现反应釜的导热油供给和配料供料的功能,实现振料、计量、下料、除尘的功能。同时接受主站的控制指令,计量相关设置值、协同配料指令,同时做出相应的应答。
一、现场总线控制概念
自动配料系统对于反应釜称重采用传统的布式I/O结构,对于导热油罐、气净化系统、采用现场总线方式。在这样方式下把以上三个上料系统根据配料机中的单体进行现场小型PLC控制和电气控制,由现场的PLC完成单体功能控制和电气操作,而由上一级PLC实现生产过程工艺协作控制。现场PLC子配料系统和上一级PLC通过通讯进行连接。
从实际意义上说,该混料机不是完全的现场总线方式,而是借鉴了现场总线的现场智能控制的理念,因此称为现场总线控制。
二、方案的提出基础和可靠性分析:
这一方式的提出示在现场设备得特点的基础上提出来的。反应釜自动化主要有反应釜称重、反应罐、框槽配料、布袋、导热油反应罐等系统组成。在以上喂料系统中,从设备功能和分布角度,可以分成两大类:
1、适合分布式I/O结构的设备
第一类就是由众多单一功能元件或装置组成的配料系统。如反应釜称重配料系统和反应罐上料系统都属于第一类。这一类具有这设备分散功能单一且各不相同的特点。同时这些设备中都有着复杂的配料系统,不适合配料和现场设备就近安放的特点。
对于这些上述设备,仍然采用分布式I/O结构。
2、适合现场总线结构的设备
第二类是由综合功能设备组成的配料系统。这一配料系统都具有着有诸多功能相同的设备组成。他们统一在反应釜生产的总体框架下,同时他们又相对独立,每个分单元都是个完整的小配料系统。如框槽配料、气净化(布袋)、导热油反应罐。这些设备适合采用现场总线控制方式。下面是详细地说明:
2.1导热油反应罐系统:
导热油反应罐配料主要有若干(一般3~4)个导热油罐单体和恒温设备、公共阀门组成,实现反应釜的导热油供给。在导热油反应罐配料系统中,每个单体都有相同的设备构成,每个导热油反应罐都是完整独立的功能单元,都能够实现搅拌反应罐、送油的任务;同时他们又统一在导热油反应罐生产的工艺之下,共同配合完成反应釜的导热油供给工作。另外从设备配置上各个导热油反应罐无论是仪表还是电气设备配置相同;
2.2反应罐气净化(布袋)系统:
该投料机有若干布袋和总管设备组成,完成反应罐气的净化以及往导热油反应罐供应干净的罐气。其中组成中的各个布袋单体都是个完整独立的功能单元,有相同的设备构成,都能够实现净化、反吹、出料、送气的任务;同时又都统一在布袋配料对反应罐净化、往导热油送保温状态的生产工艺之下。
2.3框槽系统:
这一配料系统由输料皮带组、液压站、供料设备组组成,实现反应釜配料供料的功能。其中供料设备组由料仓、下料给料机、下料振筛、计量仓、下料液压闸门除尘阀门构成,完成独立的物料筛分、计量任务、供料功能、工程除尘。并统一在反应釜配料制度之下协调工作,共同完成反应釜供料的生产任务。
正是因为以上三个配料系统的这些特点,为三配料系统的现场总线的控制方式提供了应用前提。从而和反应釜本体仪表、反应罐的配料系统共同构成了“反应釜现场总线控制加分布式I/O结构的自动化配料系统”。
3、硬件实现
喂料系统总的自动化配置结构仍然保留现有的结构,采用三个CPU,分被控制反应釜本体、反应釜供料、布袋系统。同时对于每个配料针对实际情况,采用完全分布式I/O结构和现场总线加分布式I/O结构。其中反应釜本体采用分布式I/O结构、反应釜供料中的反应罐控制部分(含液压站)采用分布式I/O结构、反应釜供料中的框槽配料部分采用现场总线方式、导热油反应罐和布袋采用现场总线方式。具体配置如下:
3.1框槽配料:
和反应罐共用一个主站CUP,并按照仓组数量设置相应的S7200PLC子站。各个子站通过通讯和主站CPU进行通讯实现数据交换。
主站功能:
完成各个仓组的计量设置、配料指令发布
子站功能:
各子站中实现:振料、计量、下料、除尘的功能;同时接受主站的控制指令:计量相关设置值、协同配料指令,同时做出相应的应答。各子站分别设置独立的控制箱,箱内集成PLC配料系统、低压系统、仪表计量系统。各控制箱放置在现场。同时皮带组单独作个子站。
该配料系统共有如下S7200子站:
振料子系统11套(现场采用14个计量仓)
皮带输料系统:1套
3.2反应罐气净化(布袋)系统:
和导热油反应罐配料使用同一个主站CPU,并设布袋单体S7200PLC子站、公共阀门S7200配料系统、出料系统S7200子站。子站间通过通讯和主站CPU进行数据交换。